What is FSMA 204 and How Does It Apply to RFID Technology?
What is FSMA?
Overview of the Food Safety Modernization Act (FSMA)
The Food Safety Modernization Act (FSMA) is a pivotal legislation in the United States that was signed into law on January 4, 2011. It represented the most comprehensive reform of the nation’s food safety laws in over 70 years. Prior to FSMA, the Food and Drug Administration (FDA) was primarily reactive, dealing with food safety issues as they arose. FSMA was introduced in response to several high-profile foodborne illness outbreaks that had significant public health and economic impacts.
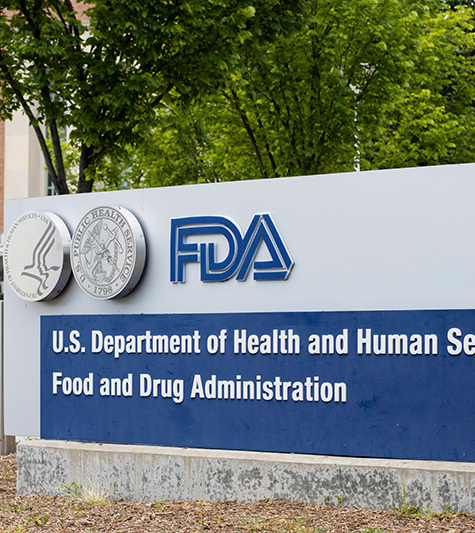
FSMA's core focus was aimed to shift regulations from reaction to prevention, taking proactive steps to prevent foodborne illnesses before they occur. This evolution in approach was deemed necessary in a world with increasingly complex food production and logistics systems that spanned globally.
New FSMA Regulations: FSMA 204
The FSMA has been pivotal in shaping regulations aimed at ensuring the safety of the food supply in the United States. One of the latest updates making waves is FSMA 204, a new ruling that came into effect in January 2023, which introduced some new and significant changes such as enhanced traceability for high-risk foods. The goal is to quickly identify and respond to potential sources of contamination, thereby reducing foodborne illness outbreaks.
FSMA 204 emphasizes the need for an end-to-end traceability system that links everyone in the supply chain—from growers to processors, distributors, and retailers. This rule requires detailed record-keeping for effective tracking of food products. The idea is that with better traceability, the FDA can more efficiently trace back any contaminated foods to their source and eliminate them from the supply chain as quickly as possible.
What's particularly exciting about FSMA 204 is its encouragement of technology adoption across the food industry. By leveraging innovative solutions, businesses can streamline compliance and enhance their operational efficiency.
As FSMA 204 prioritizes traceability across the supply chain, there are multiple ways to comply. The requirements set down by FSMA 204 include:
- Implementation of a food traceability program
- Emphasis on maintaining records of key data elements (KDEs) for specific critical tracking events (CTEs)
- The ability to share this information with the FDA within 24 hours of a request (1)
The one important factor that is not outlined by the FDA is how food manufacturers, distributors, resellers, or restaurants have to accomplish compliance. No one technology or one workflow is required by the FDA, which opens the door for supply chains to adopt RFID technology to not only comply with FSMA, but also to increase inventory accuracy and supply chain visibility.
RFID Technology to Meet FSMA Standards
Ensuring FSMA Rule 204 Compliance with RFID Technology
Integrating Radio Frequency Identification (RFID) technology within the supply chain is increasingly proving to be an effective strategy to meet the Food Safety Modernization Act (FSMA) standards. In this context, RFID technology becomes vital by offering enhanced tracking and data reporting capabilities.
RFID technology is utilized by attaching small tags on product packaging that are encoded with a unique ID that is associated with information about each product. This data can be read at various points along the supply chain, enabling real-time information flow. For FSMA compliance, RFID tags can be read at key events (called Critical Tracking Events, or CTEs) such as points of manufacture, refrigeration, logistics/transportation, and entering or exiting a building. Creating RFID tag read points for CTE’s supports rapid access to product origin, manufacturing details, and logistical timestamps—crucial for tracing the movement of goods and swiftly addressing potential safety issues.
Benefits of Using RFID in the Supply Chain
The implementation of RFID technology offers numerous benefits to the supply chain, particularly with regard to ensuring food safety and maintaining FSMA compliance:
- Enhanced Traceability: RFID provides the ability to precisely track products from origin to destination, enabling improved accuracy in tracing any contamination source. It simplifies the recall process by identifying only affected items, thus minimizing disruption.
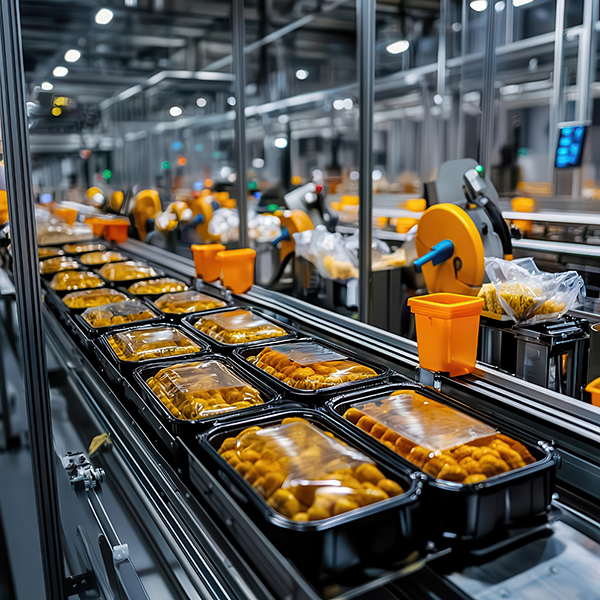
- Improved Efficiency: Automation in data capture reduces human error and boosts operational efficiency. This technology cuts down the time required for inventory checks and stock takes while maintaining accuracy in data reporting.
- Real-Time Monitoring: RFID facilitates continuous, real-time monitoring of products in storage conditions, which can be linked with temperature and humidity data. This function is crucial in maintaining the quality and safety of perishable goods.
- Data Integration: With RFID, data can be seamlessly integrated into existing management systems, improving coherence and collaboration across the supply chain. Access to historical data also strengthens predictive analytics to preempt potential problems.
Success Stories: FSMA Compliance with RFID
Several organizations have successfully integrated RFID technology to comply with FSMA regulations, showcasing the transformative potential of such systems. For instance, a global food distributor implemented an RFID-based traceability system that led to a 30% reduction in product recall times. This improvement not only fulfilled FSMA requirements but also boosted the company's reputation for reliability and safety.
Another success story is a dairy company that adopted RFID technology to monitor and maintain cold chain compliance. This enabled precision in controlling storage temperatures, significantly minimizing spoilage and ensuring that products reached consumers fresh and safe.
Chipotle, a restaurant chain, piloted RFID technology for traceability, and when it was successful, then “essentially asked all our suppliers” to tag products with RFID.(2) Chipotle started testing RFID with the food products with the quickest expiration dates from a unique group of suppliers, such as meat, dairy, and avocados. Because Chipotle has seen such success with inventory management, they are encouraging more of their suppliers and vendors to jump on board in order to improve their own inventory management in addition to food traceability.
Embracing RFID for FSMA compliance offers companies and their suppliers a competitive advantage while aligning with the robust standards set forth by the FSMA.
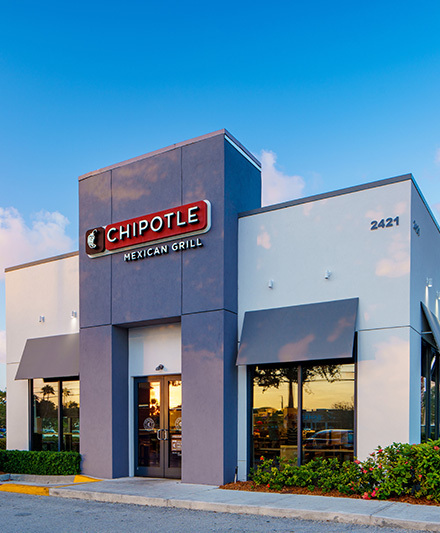
Conclusion
For more information on how food growers, manufacturers, distributors, suppliers, retailers, and quick serve restaurants are deploying RFID technology for FSMA compliance, contact us!
- (1) https://www.fda.gov/food/food-safety-modernization-act-fsma/fsma-final-rule-requirements-additional-traceability-records-certain-foods#:~:text=Additional%20Requirements%20(%C2%A7%201.1455),other%20threat%20to%20public%20health
- (2) https://www.supplychaindive.com/news/chipotle-rfid-restaurant-inventory-tracking/650884/